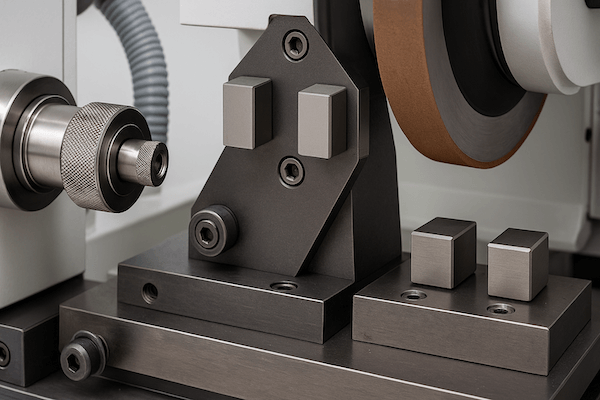
Tungsten Carbide Tools for Grinding Equipment Applications
Tungsten carbide plays a critical role in the grinding process by providing exceptional hardness, wear resistance, and dimensional stability under high loads. In high-precision environments such as cylindrical grinding, centerless grinding, and tool grinding, these carbide components improve process consistency and tool life. Below is a detailed overview of key tungsten carbide products designed specifically for grinding equipment applications.
Typical Tool Types of Tungsten Carbide in Grinding Equipment
In grinding equipment, tungsten carbide tools are mainly used for high-precision machining, grinding and dressing of high-hardness materials. Its excellent wear resistance and high hardness make it the first choice for heavy-duty grinding, profile grinding and dressing tools. The following is a classification of the common applications of tungsten carbide tools in grinding equipment:
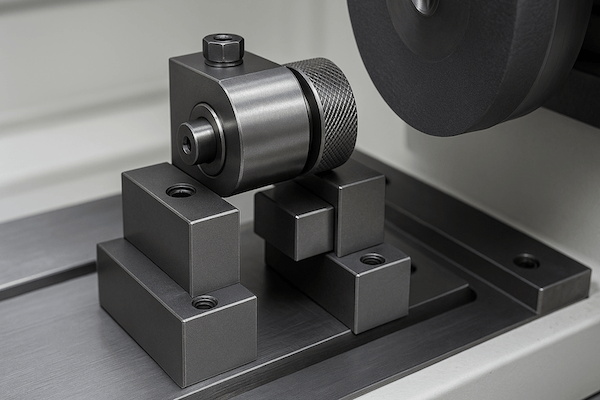
Carbide Dressing Rollers
High-hardness rollers used for forming and reshaping grinding wheels in CNC and conventional grinding machines.
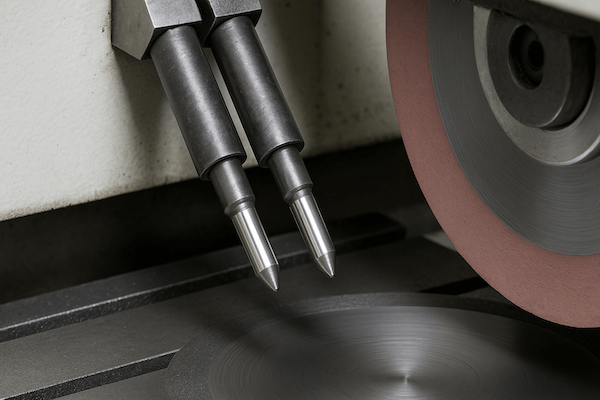
Carbide Dressing Pens
Handheld or fixed-point tools for restoring wheel profiles during fine surface finishing or precision grinding operations.
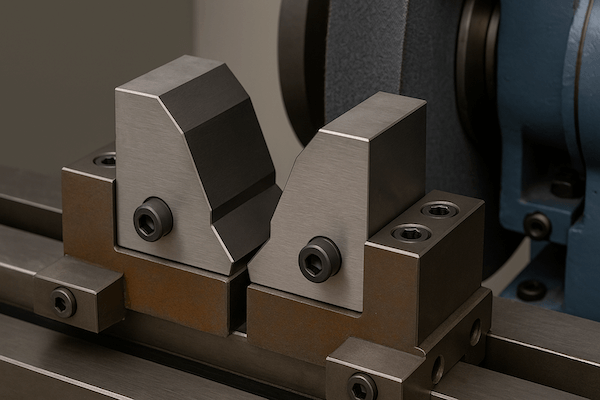
Carbide Guide Blocks
Precision alignment blocks that guide parts during centerless or through-feed grinding operations with minimal wear over time.
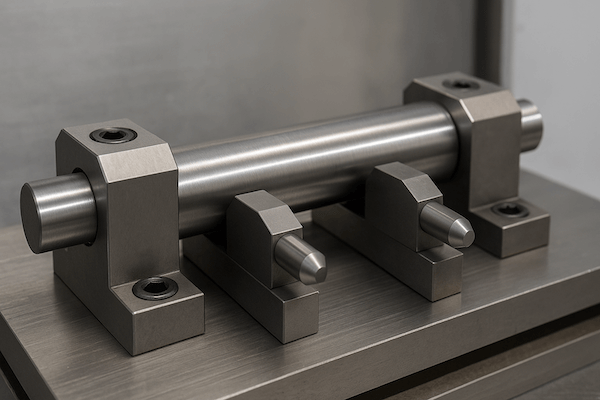
Carbide Clamping Jaws / Inserts
Wear-resistant jaws or inserts used in grinding fixtures to secure components during high-precision machining.
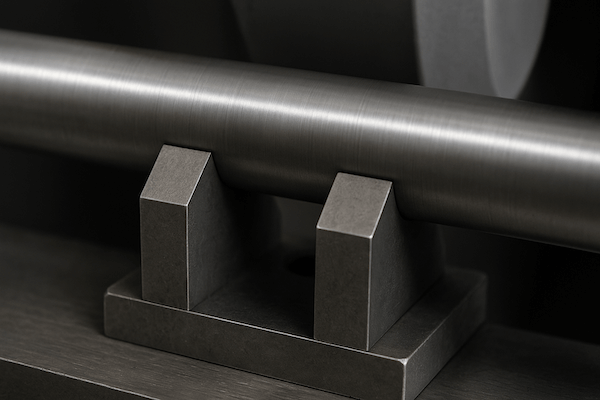
Carbide Support Pads / Rest Pads
High-stiffness pads supporting parts during internal or external grinding to ensure precision geometry.
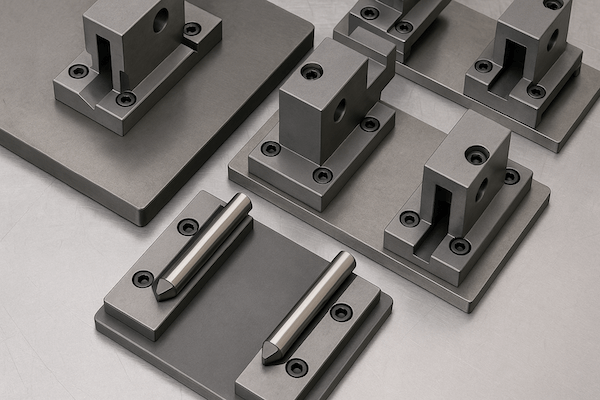
Carbide Base Plates
Hard-wearing structural bases installed in grinding fixtures or tool holders for dimensional stability.
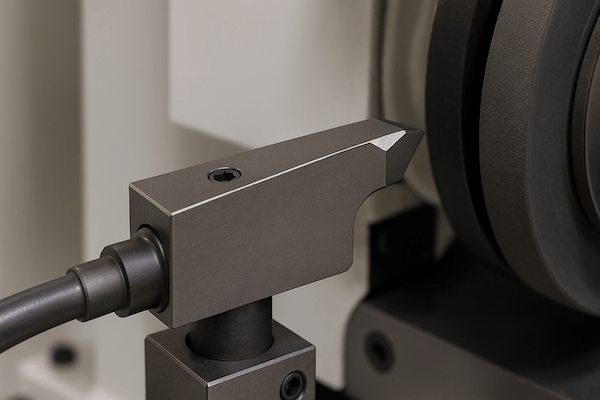
Carbide Wheel Tool Holders
Rugged holders used to position grinding wheel dressers with repeatable accuracy and long-term reliability.
Quick and easy: Enter your specifications and get a quote in one business day
Applications of Tungsten Carbide Tools in Grinding Equipment
Tungsten carbide components provide exceptional durability, accuracy, and reliability across various grinding systems. Whether maintaining tight tolerances or supporting high-volume production, carbide tools are essential for maximizing productivity and tool life in grinding equipment.
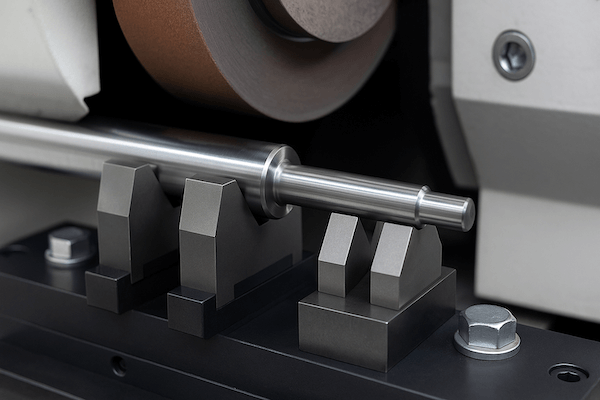
Centerless Grinding Machines
Tungsten carbide guide blocks and rest pads are used to support long, cylindrical shafts during through-feed and in-feed centerless grinding. These components ensure stable part transport and minimize vibration, resulting in consistent surface finish and dimensional precision.
Advantages:
-
Superior wear resistance under continuous material feed
-
Smooth, vibration-free guidance for long shafts
-
Ideal for high-volume shaft production in automotive and bearing industries
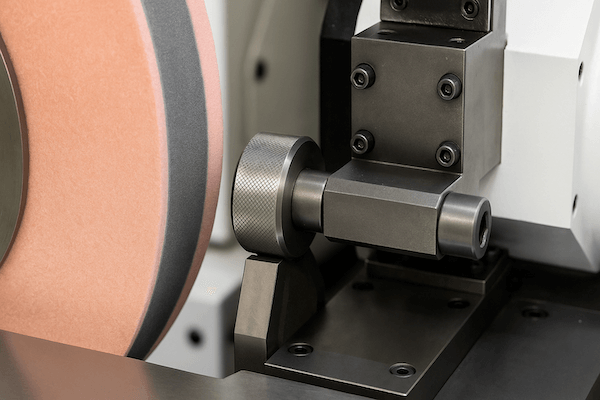
CNC Cylindrical Grinding Machines (OD Grinding)
Tungsten carbide dressing rollers are used to regenerate the grinding wheel profile after each cycle, ensuring it maintains the desired shape and cutting properties. They are essential for high-precision outer diameter (OD) grinding processes.
Advantages:
-
Maintain wheel geometry with micro-level precision
-
Extended tool life with stable repeatability
-
Compatible with automated grinding cycles in high-accuracy sectors
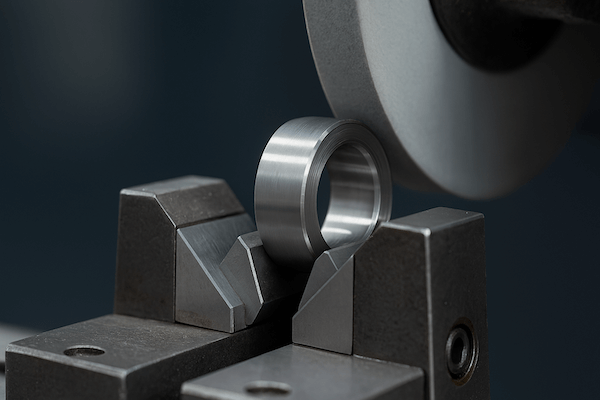
Internal Grinding (ID Grinding) Systems
Tungsten carbide rest pads and support blocks are used in internal grinding machines to precisely hold and support small-bore components during finishing. These fixtures provide rigidity and precision alignment during ID grinding of precision bores.
Advantages:
-
High stiffness for micrometer-level tolerances
-
Ideal for grinding small inner diameters or precision bushings
-
Long-lasting performance in abrasive environments
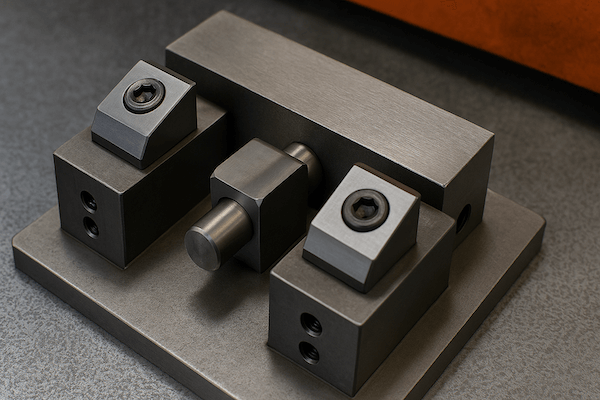
Grinding Fixture Systems
Tungsten carbide clamping inserts and fixture blocks are integrated into custom grinding jigs to hold components firmly during surface or form grinding. These inserts withstand high clamping forces without deformation.
Advantages:
-
Consistent high-rigidity positioning for grinding precision
-
Excellent wear resistance under repetitive clamping cycles
-
Minimizes fixture maintenance and tool change downtime
Conclusion: Elevate Grinding Performance with Tungsten Carbide Solutions
Tungsten carbide tools are indispensable components in modern grinding equipment, delivering unmatched durability, precision, and consistency across centerless grinding machines, OD/ID grinders, and fixture systems. From dressing rollers and guide blocks to clamping inserts and support pads, each tool plays a specialized role in enhancing grinding efficiency and achieving high-precision results.
By integrating tungsten carbide components tailored to each grinding application, manufacturers can significantly reduce tool wear, minimize downtime, and maintain exceptional part quality over long production runs. Whether you’re processing small bores, long shafts, or high-tolerance surfaces, carbide tooling ensures maximum performance and reliability under demanding conditions.
Quick and easy: Enter your specifications and get a quote in one business day