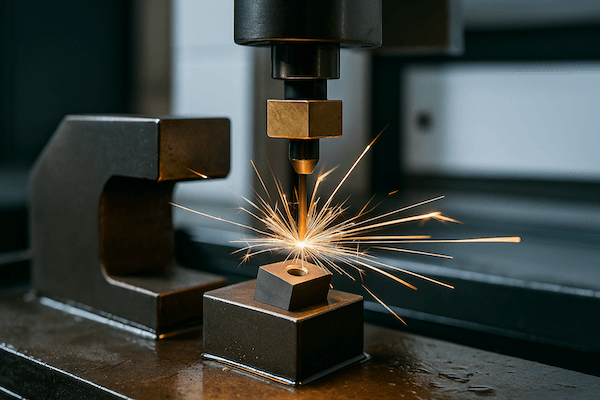
E.D.M. Capabilities
Electric Discharge Machining (EDM) has transformed the manufacturing capabilities of tungsten carbide tools. As a specialized producer, we apply advanced EDM techniques to achieve intricate designs, unmatched precision, and tailored solutions. In this article, we'll share our EDM expertise, helping customers and industry peers understand its essential role in carbide tool production.
Expertise in Electrical Discharge Machining
Retop Carbide has an excellent reputation as a quality source for EDM capabilities of tungsten carbide parts.
Main EDM Types and Equipment
Type | Electrode | Dielectric | Typical Use in WC Tools |
---|---|---|---|
Sinker EDM | Solid Cu, graphite, Mo | Oil-based fluid | Complex cavity molds, chamfers, micro-features |
Wire EDM | Continuous brass wire | Deionized water | Cutting thin rings, slots, precision profiles |
Micro-EDM | Micromachined electrodes | Specialized fluid | Drilling coolant holes (Ø0.2–1 mm), fine detail |
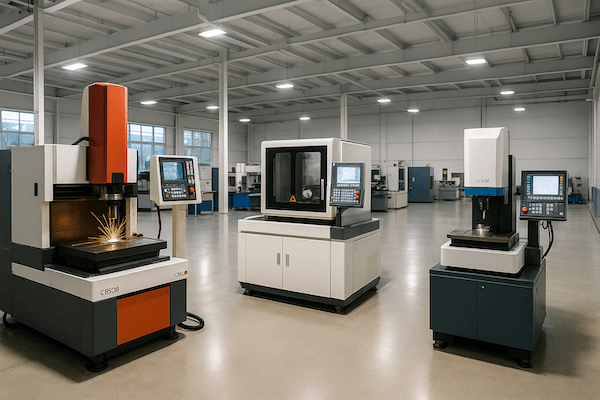
Understanding the Fundamentals of EDM
Principle
1. High-frequency electrical pulses generate controlled sparks between an electrode and the workpiece, locally melting/vaporizing material.
2. No mechanical cutting forces—ideal for ultra-hard materials like WC–Co.
Process Cycle
1. Servo Gap Control: Maintain a microscopic gap (~3–100 µm) via servo feedback.
2. Pulse Generation: Apply voltage pulse (Ton), then wait interval (Toff).
3. Spark Discharge: Material removal by repeated micro-sparks.
4. Debris Flushing: Dielectric (oil or deionized water) carries away molten debris.
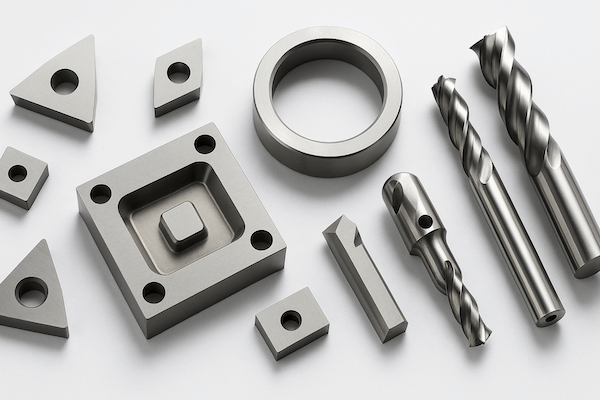
Why EDM is Essential in Tungsten Carbide Tool Production
Tungsten carbide’s extreme hardness and wear resistance pose significant machining challenges. Traditional mechanical machining processes struggle with efficiency and precision. EDM overcomes these limitations, allowing us to shape carbide without mechanical stress, ensuring structural integrity and precise geometry.
Quick and easy: Enter your specifications and get a quote in one business day
Types of Tungsten Carbide Tools Produced Using EDM
Our combined EDM portfolio handles everything from large-scale cavities to micro-features in a single setup.
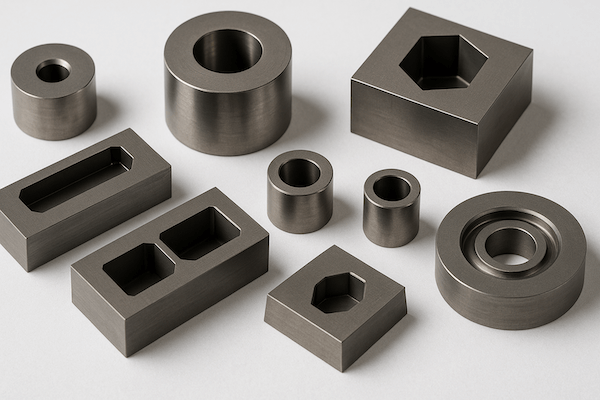

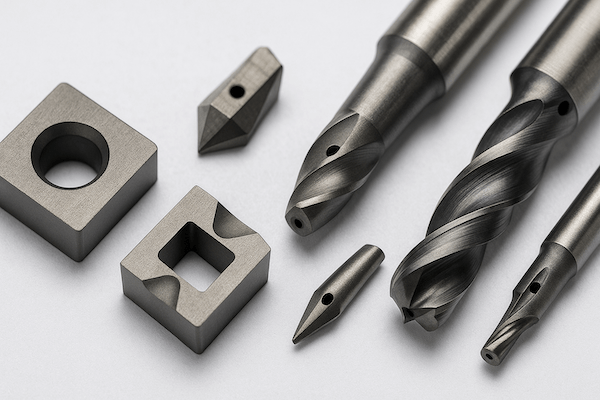
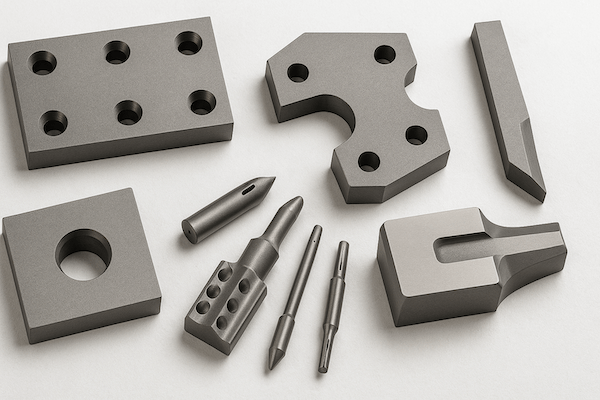
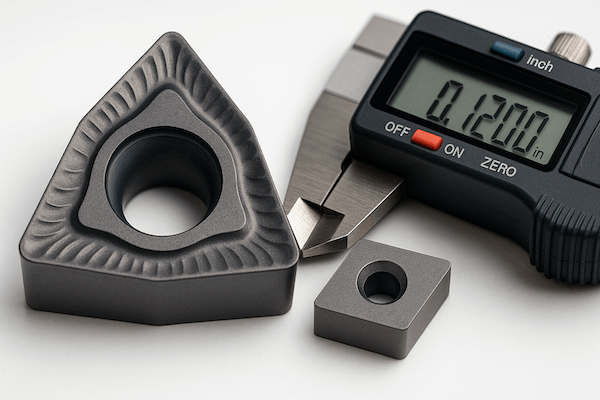
Precision and Complexity: How EDM Makes a Difference
EDM enables us to achieve exceptional complexity and tight tolerances:
1. Minimal tolerance variance (±0.005 mm) on intricate profiles.
2. Ability to produce precise internal features and delicate microstructures without cracking or deformation.
3. Consistent reproducibility of complex geometries in high-volume production runs.
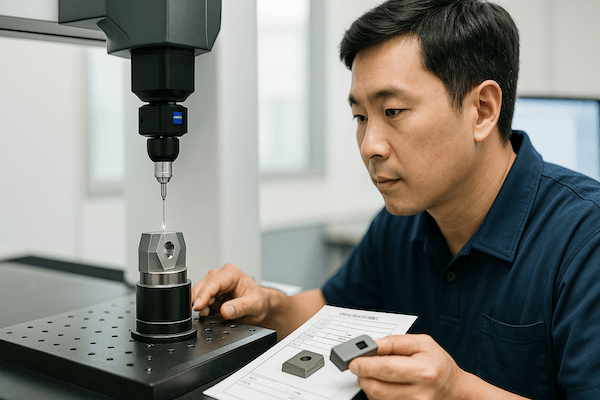
Quality Control Measures in Our EDM Process
Quality is paramount. Our rigorous EDM quality control process includes:
1. Surface finish inspections (Ra ≤ 0.4 µm).
2. Microscopic analysis to detect and remove recast layers and micro-cracks.
3. Dimensional verification through advanced Coordinate Measuring Machines (CMM) and optical metrology systems.
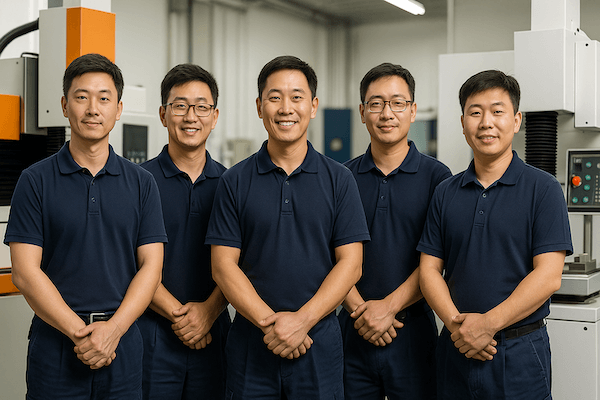
Why Partner With Us for Your EDM Tungsten Carbide Tools?
Choosing our EDM capabilities provides significant advantages:
1. Expert operators with years of specialized experience.
2. State-of-the-art EDM machines ensuring superior precision and efficiency.
3. Flexible production capabilities to accommodate any custom tooling request.
4. Uncompromising quality assurance, ensuring consistent performance and reliability of your tools.
Conclusion
By integrating Sinker, Wire, and Micro EDM into your tungsten carbide tool workflow—combined with rigorous parameter control, electrode management, and post-EDM quality checks—you achieve the precision, surface integrity, and complex geometries demanded by today’s high-performance cutting tools.
Quick and easy: Enter your specifications and get a quote in one business day